What Maintenance Does Your Machine Tool Need?
20 Aug 21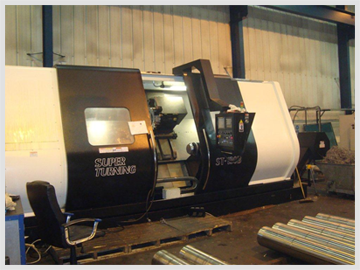
You’re thinking of investing in a Computer Numerical Control lathe or milling machine for your manufacturing processes. Is there anything you need to consider before you make your new purchase? Well, not only do you need to consider running costs, but you’ve got to be prepared to service your machining tool too. There are routine checks you need to complete to analyse and track the health of your machine, on top of professional servicing!
With all of this in mind, what maintenance does your machining tool need? And can you complete any of your care independently? We’ve got all the answers at DTS UK in this guide below.
Planned Professional Maintenance Annually
Annual planned maintenance can extend the lifetime of your machining tool by years. When you seek a team of highly experienced technicians, you’ll benefit from thorough diagnostic processes to identify issues that you may not have spotted alone. Spotting technical issues before they escalate solves the core of the problem in your machining tool rather than leaving you to treat the expensive symptoms.
Through careful machine tool maintenance, your manufacturing can remain consistent and precise with your highly sophisticated equipment. Due to the complexity of modern lathes and milling machines and their new processes, performing your big maintenance tasks with a professional is much more sensible than attempting DIY. Even manual lathes and their many parts can pose a challenge to service if you’re inexperienced, so be sure to seek expert help for your peace of mind.
Day-To-Day Care and Caution
Your day-to-day treatment of your machining tool will largely determine the health of your machining tool. Neglected machines that are left to run for hours on end without any aftercare will rapidly decline.
Things to assess regularly with your CNC machine:
- Lubrication. Busy lathes and milling machines have parts that can rub against one another and cause abrasion without regular lubrication. Any moving part of your tool ought to be lubricated to reduce wear and tear. You ought to grease both internal and external elements that you can reach.
- Alignment: Your engineers should conduct occasional tests to measure the size of components being created by your machining tool. If the measurements are incorrect compared to the coding, your machining tool is incorrectly aligned and needs recalibrating.
- Appearance. Routine inspection from your operators guarantees that your team is familiar with the structure of your machine. If anything looks out of place, they’re likely to notice it and request a repair before attempting to use the tool.
- Cleanliness: One of the most critical steps in maintenance is cleaning your machining tool. Your parts are made with metal and can accumulate grime, rust, and dust faster than you’d anticipate. Regular cleaning prevents the material in your machine from deteriorating.
Reactive Repairs When Necessary
Even with the closest care and consideration, your machining tool can break down. Parts can quickly become unaligned, and the electronics of your machine can malfunction. You’re never guaranteed that your machining tool will be immediately fit to use. Should your CNC lathe or milling machine be displaying an error message, or if it appears to have entirely broken down, you need a reactive repair.
Reactive repairs respond to problems when they’ve occurred, so they’re less preventive than your other methods of maintenance. However, they’re just as vital to machine health because if you ignore the need for repair, the state of your machine will only worsen. Perhaps to the point of becoming a danger to employees. Contact us at DTS UK if you require an emergency repair of your machining tool or you’re searching for a provider of professional planned maintenance on lathes and milling machines.