Milling machine NORMA MG installed at Chelburn Precision
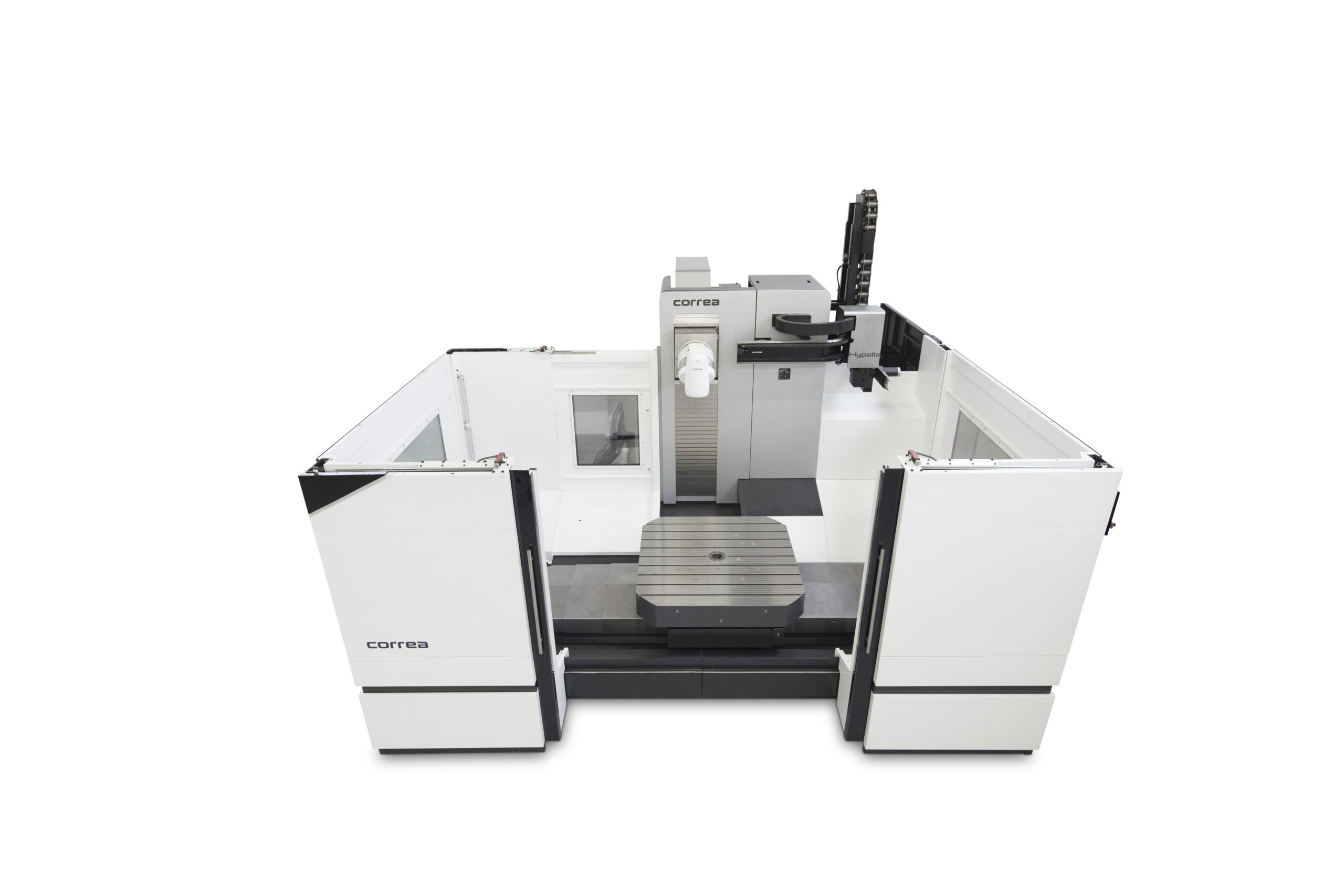
Case Studies
The company supplies precision machined components to some of the world’s most demanding markets. Chelburn manufactures highest quality components for several industries including: Oil and Gas, Aerospace, Paper Converting Equipment, Can Making Machines and Mining Equipment.
For manufacturing components with the highest quality Chelburn Precison has just had installed a large capacity universal milling machine, Correa Norma MG-35 with a capacity of 3500 mm x 1250 mm x 1500 mm; which is the fifth Correa machine purchased by the firm.
The NORMA MG with lateral ram offers robustness thanks to its ram guiding system in L; its rotary table is completely integrated in the machine’s kinematics to work in 4+2 axes.
Managing Director, Neil Travis explains that “it made sense to go for another Correa. They are accurate, reliable and we have had success with several of the Correa brand of tool already. It gives us great confidence to know that our highly skilled members of staff are able to work to the tightest of tolerances on this machine tool. The ability to meet our customer´s specification in terms of dimension, surface finish and just as importantly, timescale, is key to our success.”
You can watch the timelapse of NORMA MG’ installation at Chelburn’s workshop on this link.
Bendalls Engineering enhances its productive capacity with a FOX-60

Bendalls Engineering was founded in Carlisle, Northern England, in 1894 as a family-owned business, they design and manufacture for the nuclear, Renewables, Oil & Gas, Petrochemical, Pharmaceutical and Process industries. In 1996, Bendalls was bought by Carr’s Group PLC, and became an essential part of the expanding Carr’s Engineering Division. Its operational base, as of 2006, is a purpose-built 5000 square metre engineering facility and employs 85 people, it is specialised in the design and manufacture of pressure vessels and steel fabrications.
Today, Bendalls Engineering continues to invest in the latest technology to deliver premium services to clients. Managing Director, Sean Sunders, explains that quality is at forefront of their business especially relevant in oil and gas and nuclear industries; they have recently acquired a bridge type machine FOX for the precision machining of large components. Its investment in Correa milling machine allows that the whole manufacturing process is performed at its facilities, guaranteeing the highest quality and delivery times to Bendalls’ customers.
The milling machine has travels of X 6000, Y 4250 and Z 1750 mm and table dimensions of 6500 mm x 2500 mm with maximum width between columns of 3750 mm, a table capacity of 25 Tn. It also features a Renishaw compact touch probe for setting, in cycle part measurement, inspection and verification of components with automatic data recording to improve the efficiency of the productive process.
The head technology is another strong point of Correa milling machines for Bendalls; the UAD with rotation every 0.02o thanks to the double Hirth coupling system, patented worldwide; it offers 6000 rpm with no limitations and a maximum coupling repeatability error of ±3”.
Mark Johnson, Production Manager at Bendalls Engineering, explains that the FOX has allowed the company to go for larger projects due to machine’s capabilities and guarantee higher quality standards. This larger machine give company a differentiation element from competitors as they can offer a wider range of components.
Original content from MTD CNC.
Watch the videos of Bendalls Engineering recorded by MTD CNC
Johnford ST130 at Xcel Superturn
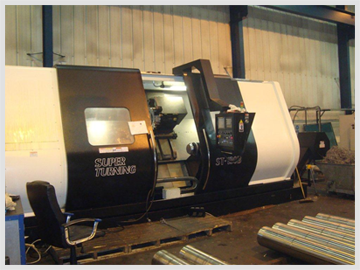
It’s always pleasing to hear a ‘good-news’ story in the UK machining industry and just such a ‘good-news’ label can certainly be applied to the latest news emerging from X-Cel Superturn, the Yorkshire-based global manufacturer of precision machined components. X-Cel Superturn specialise in producing precision machined components and predominantly support the petrochemical (including down hole drilling, surface, and subsea applications) and power generation industries.
Recent exponential business growth has been experienced to the point that 40% cent of the company’s turnover today is driven through exports to Brazil, Asia and the US and this has, in turn, encouraged the group to invest in new state of the art CNC Machinery to supply its ever growing and flourishing customer base. Currently the group has over 100 employees spread across three sites in Yorkshire (X-Cel AMP, X-Cel Atlas, and X-Cel Precision) and one in Houston (X-Cel USA) supplying precision engineered components to the oil and gas industries.
With their USA base located strategically close to most of the Oil and Gas OEM’s in Houston, X-Cel Superturn have ready access to clients who are eager for their ‘Down Hole Tools’ for drilling in oil wells and gas fields. These ‘Down Hole Tools’ are manufactured from high nickel content materials which can be tough to machine due to the nature of the material. At their manufacturing facility in Sheffield they have a wide range of machines for the manufacture of these tools, including VMCs and HMCs and both small and large turning centres.
Recently X-Cel Superturn decided to invest in a new lathe and they turned to regular supplier, Chorley, Lancs, based Design & Technical Services Ltd (DTS) for advice to help them make that purchase. X-Cel Superturn MD Andrew Taylor had already carried out his own market research and was considering purchasing the Johnford ST 130 equipped with a 3 metre bed length that would enable his business to turn larger and longer parts between centres.
As part of the evaluation process, DTS arranged that they accompany Andrew and travel over to Paris to observe an end-user working with a similar machine, in order that Andrew could gain unbiased, first-hand input on the capabilities of the machine. Upon his return Andrew placed an order for the Johnford ST 130 – having been convinced it was ideal for their manufacturing plant.
Andrew comments, “The Johnford ST 130 machine was extremely well built and this is really important to us as we can take heavy cuts on difficult materials when turning our ‘Down Hole Tools’. The trip to France proved to me that this machine was just right for us.
It was also a contributory factor in reaching my decision that DTS were to be our supplier, as we’ve bought Correa bed mills from them in recent years and been extremely impressed with not only the product but the DTS support and back-up too, which we’ve always found excellent. We did compare and contrast the Johnford ST 130 lathe with other manufacturers before we ordered but ultimately felt that the technical capabilities and the cost of the Johnford machine far outweighed all other competitor products”.
In conclusion and on a lighter note: – it’s not always about ‘drilling’ for profit for Andrew Taylor and X-Cel Superturn, on the odd occasion they get a chance to be charitable too. In August 2102 they were approached by TASTE, a charity that works to give rural communities access to safe drinking water. Andrew Taylor explains further: “TASTE approached us to see if we had any used drill bits that we could donate to them. Once they’d explained what the charity was about and how they help communities in Nigeria, we found what they do so interesting and worthwhile, we decided it would be better to provide three new drill bits instead. One of these drill bits will bore up to six 30 metre holes, as each of these boreholes provide water for around 2,000 people, the collaboration looks set to improve the living standards of thousands of families in Nigeria”.
Ben Udejiofo, chief executive of TASTE said: “We are so grateful that a significant company like X-Cel Superturn is keen to work with a small charity like TASTE, but through similar partnership with other companies, TASTE could help many more communities thousands of miles away”.
New Geminis GT5i
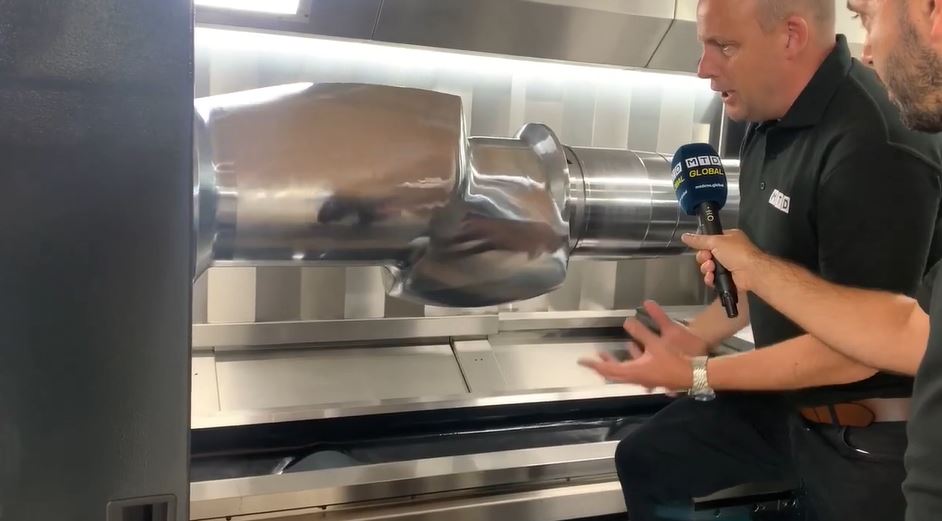
Geminis with there pedigree in flat bed lathes have now reinvented there current flatbed lathe to offer our customers, more rigidity, more technology, bigger headstock, bigger weight carrying capacity, rack and pinion throughout.
Catch the latest update here at EMO 2019
Destec Engineering Op's for 6 Axis Machine Norma MG
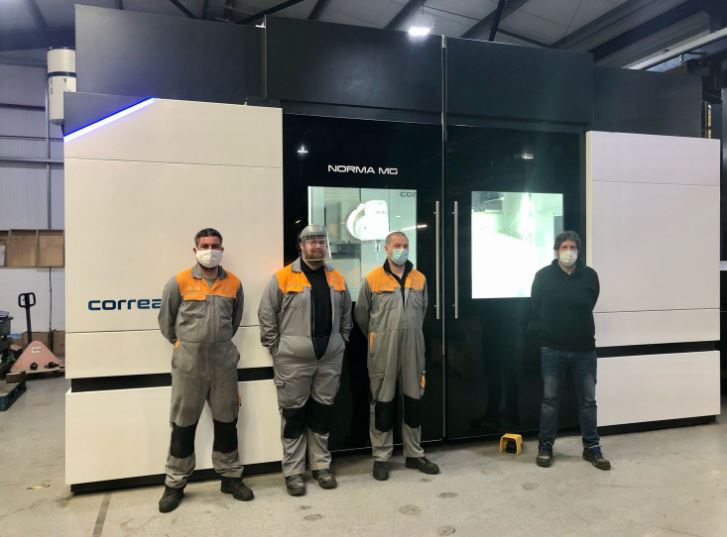
Destec provide high containment solutions to the Oil and Gas industry. They are now on there multi face machining journey with there Correa Norma MG, this 6 axis milling machine will now allow Destec to combine all machining operations on there pipe connectors, seal rings and valve blocks into one operation. Reducing lead time, Cost, machining time and improving quality has made this project a great success for all involved.
Prior to receiving there Norma MG the majority of there parts could take 3 to 4 operations where now the are reduced to one.
Watch Video